
Greener life science labs: the challenge to save energy and reduce waste
How to decrease the environmental footprint of a life science research centre? Annegrät Daujeumont shares how following a certification programme can help labs embrace sustainability and eco-friendly practices
Research management
Sponsored by
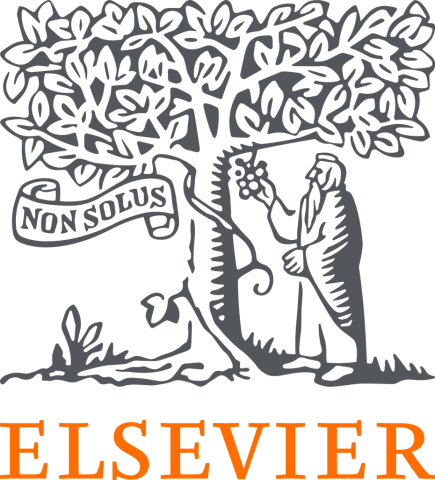
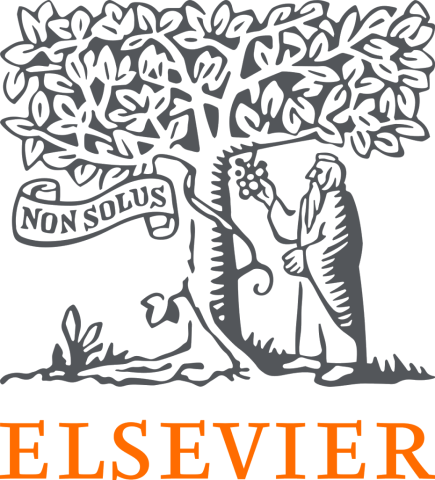
Elsevier helps researchers and healthcare professionals advance science and improve health outcomes for the benefit of society.
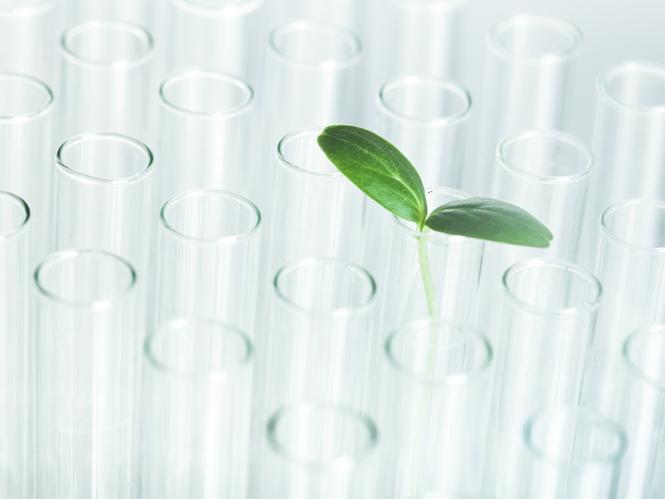
Life science research activities go through an astronomical amount of plasticware – about 5.5 million tonnes per year worldwide. Practices such as waste-sorting directly in the laboratories are part of greening the lab but are not the only eco-friendly practices that laboratories can employ. The lab support team at the Luxembourg Centre for Systems Biomedicine (LCSB) of the University of Luxembourg has prioritised sustainability since the centre was founded in 2009. Repairing instead of replacing, choosing equipment with low energy consumption and having efficient chemical inventory software are only a few examples of initiatives already in place.
But we felt that we could do even more: for example, reduce the quantity of plastic at source and optimise the use of energy-intensive equipment. We want to develop an eco-friendly attitude within the LCSB so that the effects on the environment are considered in every decision we make. To drive this behavioural change, we are implementing more structured actions and communicating as much as possible on the topic through internal channels. It is important that the whole team – researchers and lab technicians alike – understand where we are now, what we could still improve, which initiatives are under way and how each one of us can help achieve a greener lab.
- It’s a game changer: using design thinking to find solutions to the Sustainable Development Goals
- Prepare for student sustainability demands to go through the roof
- We can make research more ethical without compromising its quality
A survey to get started
The first difficulty we encountered before we could take any real action was how to assess our needs: where should we invest our energy to have the greatest impact?
To help us find an answer, we turned to My Green Lab (a non-profit organisation) and their certification programme. All team members working in the lab were invited to fill out a questionnaire. My Green Lab analysed the data and gave us an assessment. We scored quite well, particularly on topics such as fume hoods, resource management and large equipment. However, they proposed further concrete recommendations. These recommendations provided us with a framework for improvements over the next months. At the end of this process, our team will fill in the questionnaire again and a new score – corresponding to a specific certification level – will be attributed to the LCSB.
Use collaborative effort to make a difference
After establishing the framework for a sustainability project, the next step is to create a dedicated working group. At the LCSB, this group is composed of volunteers, including lab technicians and safety officers as well as scientists from different research groups. They also collaborate with central services at the university, relying on their expertise when it comes to sustainability, electricity consumption and purchases, for example. The collaborative aspect is key if you want to engage everybody when implementing new procedures and best practices.
Keep energy consumption in check
It is important to evaluate how best to use electrical equipment in the laboratories. A good place to start is to identify which instruments need to be on constantly, which can be switched on only when needed, and which can be put on timers. This assessment must be carried out on a case-by-case basis, instrument by instrument and research group by research group, in order to have the smallest possible impact on the daily organisation of the researchers and the quality of their work. Then labels can be affixed to the equipment to clearly identify when they can be switched off or if they run on timer.
The Freezer Challenge, an international competition designed to promote best practices in cold storage management, can be a good way to motivate your team to work on optimising the use of fridges and freezers. Actions can include defrosting freezers, cleaning out unneeded samples and shoring up sample-tracking methods. We emphasise two aspects: proper maintenance and sorting samples. As regular preventive maintenance was already implemented, we focused more on the second part: to discard old or unimportant samples and to reduce the number of samples stored. We now keep track of these actions and maintain an efficient inventory system. As a result, we have been able to consolidate the contents of several appliances and turn some off, extending the lifespan of our equipment and significantly reducing the energy consumption linked to cold storage.
Reuse products, limit chemicals and consider ethical sourcing
Direct reuse of some products can also help reduce waste. Consider asking suppliers if they could take back polystyrene mailing boxes and cooling packs after deliveries, for example. We are looking into solutions for empty, uncontaminated tips boxes. Although these can also be collected by some suppliers, the service is often expensive and is, for the moment, difficult to set up.
Besides the goods themselves, transportation needs to be addressed. One way to do it is to group orders and hence limit the carbon footprint. This is where collaboration with central services can come into play: we are in contact with the purchasing teams of the university to come up with solutions.
Green chemistry is another potential target for effort. A necessary step is to challenge the use of certain substances, possibly propose less dangerous alternatives that require fewer specific measures and limit energy-consuming waste treatment. Software enables us to easily identify dangerous chemicals – which are very often the worst pollutants – and we can systematically initiate a discussion between researchers and the safety officers. Together, they can evaluate if that specific chemical can be replaced with a less dangerous product, and if it is not possible, how to best use it or which prevention measures to put in place, and of course how best to plan the waste treatment stream ahead of time.
We would also like to focus on ethical sourcing of laboratory consumables such as gloves. Good production practices to consider here (and which will require proof from suppliers) include fair treatment of the manufacturer’s employees, the raw materials that are used, and the carbon footprint left by the production and transportation of these items.
The whole process takes work, of course, but the progress achieved makes it all worth it. Thanks to this recent team effort, the LCSB plans to retake the Green Lab questionnaire next September and thus be certified before the end of the year, hopefully with a certification level reflecting how eco-friendly our labs have become.
Annegrät Daujeumont is a research support technician at the Luxembourg Centre for Systems Biomedicine, an interdisciplinary research centre at the University of Luxembourg focusing on systems biology and medical research. She oversees the Green Lab certification project at the LCSB.
Research management
Sponsored by
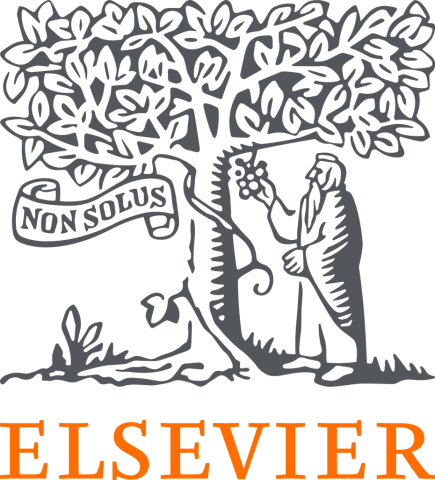