Matter
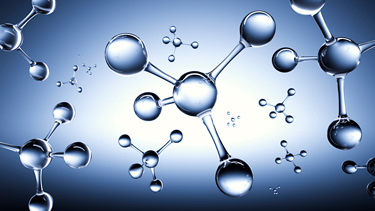
Sponsored by

Creating applicable knowledge that rewards the larger society is among the legacies that CityU seeks to achieve through its diverse disciplines. Among the more tangible benefits is the actual discovery, design and application of new materials through its faculty and researchers.
To bring this area of study into greater focus, CityU has recognised Matter as one of its five strategic themes for 2020–2025. This theme highlights the methodological study of various materials, along with the collaborative effort and insights provided by experts from all the natural sciences. Additionally, it aims to encourage innovation through practical applications in several disciplines and fields.
CityU’s competency in the field of materials science is evident in how its research teams have been able to introduce pioneering solutions to the world.
Powerful new Ti-alloys using 3D printing
A research team led by Professor Liu Chain-tsuan, University Distinguished Professor in the College of Engineering, has produced super-strong, highly ductile and ultra-light alloys thanks to the innovative use of additive manufacturing (AM), or 3D printing. The CityU-led project opens a new area in AM for the design of unprecedented titanium (Ti) alloys that are unachievable by conventional manufacturing methods and that hold great promise for a rich variety of structural applications.
The research has been published under the title “In situ design of advanced titanium alloy with concentration modulations by additive manufacturing” in the top academic journal Science. Professor Liu said, “Our alloy development team unveils the promising possibility of utilising AM to design unique heterogeneous alloys with novel microstructure and supreme properties.”
Adding microscopic materials such as iron into the mix during the AM process using this technique can make the overall alloy much, much stronger. This procedure is important because metallurgists tend to think that a lack of uniformity in alloy composition is undesirable as it leads to bad material properties. However, the team found that it can actively control the uniformity of the new alloys for advanced microstructures and properties.
The team’s research has excellent prospects for developing exciting new materials for industry.
Scientific advances in 2D/3D/4D additive manufacturing
A leading expert at CityU who developed the world’s first supra-nano-dual-phase alloy and four-dimensional (4D) ceramic printing is working on integrating these two cutting-edge technologies to fabricate lightweight, high-strength metallic materials for biomedical and aerospace applications.
Professor Lu Jian, Chair Professor of Mechanical Engineering and Director of the Hong Kong Branch of National Precious Metals Material Engineering Research Center and the Centre for Advanced Structural Materials, is an expert in the mechanical properties of metallic and ceramic materials. He is leading a team to develop a pioneering 2D/3D/4D additive manufacturing system to fabricate metallic-based materials with desired mechanical properties for different applications.
The team will first develop a 2D/3D/4D manufacturing system to create metallic-based materials with complex shapes, particularly those used in biomedical and lightweight structure applications. Since titanium (Ti-)-based alloys are considered the ideal implant material for clinical use, the team will focus on fabricating supra-nano 3D-printed Ti-based alloy and examining its mechanical properties.
In addition to 3D printing technology, Professor Lu and his team have worked on functional metallic materials, particularly their newly developed biosensing technology based on ultrasensitive surface enhanced Raman spectroscopy (SERS). This technology can be applied in areas such as antibiotics detection and food and cosmetics product safety. The team is working on the feasibility of applying the technology for the rapid detection of Covid-19, cancer and cardiovascular diseases, as well as for the non-invasive detection of diabetes.
Understanding complex materials through neutron scattering
An expert in neutron scattering measurements at CityU has applied this state-of-the-art experimental technique to identify the deformation and transformation behaviours in complex materials, in particular at ultra-low temperatures, opening up a new area of materials research.
“Neutron scattering is like a giant microscope that can reveal the structure and dynamics of a material, such as how atoms are packed and how they move,” explained Professor Wang Xunli, Chair Professor and Head of the Department of Physics, and also Fellow of the Neutron Scattering Society of America.
For example, experimental studies on the physical properties of amorphous materials have been very difficult to conduct owing to their disordered atomic arrangement. But using the neutrons scattering technique, Professor Wang led an international research team to overcome this challenge, and measured the atomic dynamics in zirconium-copper-aluminium metallic glass.
Using the neutron-scattering instrumentation, Professor Wang and his team discovered that high-entropy alloys (HEAs), a new class of structural materials consisting of multiple principal elements, exhibit exceptional mechanical properties at ultra-low temperatures owing to the coexistence of multiple deformation mechanisms. The CityU team has revealed for the first time the sequence of deformation mechanisms in HEAs at ultra-low temperatures, opening up new terrain that very few have examined.