Green steel revolution: How Swinburne researchers are shifting steel manufacturing towards net zero emissions
Swinburne researchers are investigating ways to decarbonise the steel-making process using magnetite ores, hydrogen, ammonia, and renewable electricity.
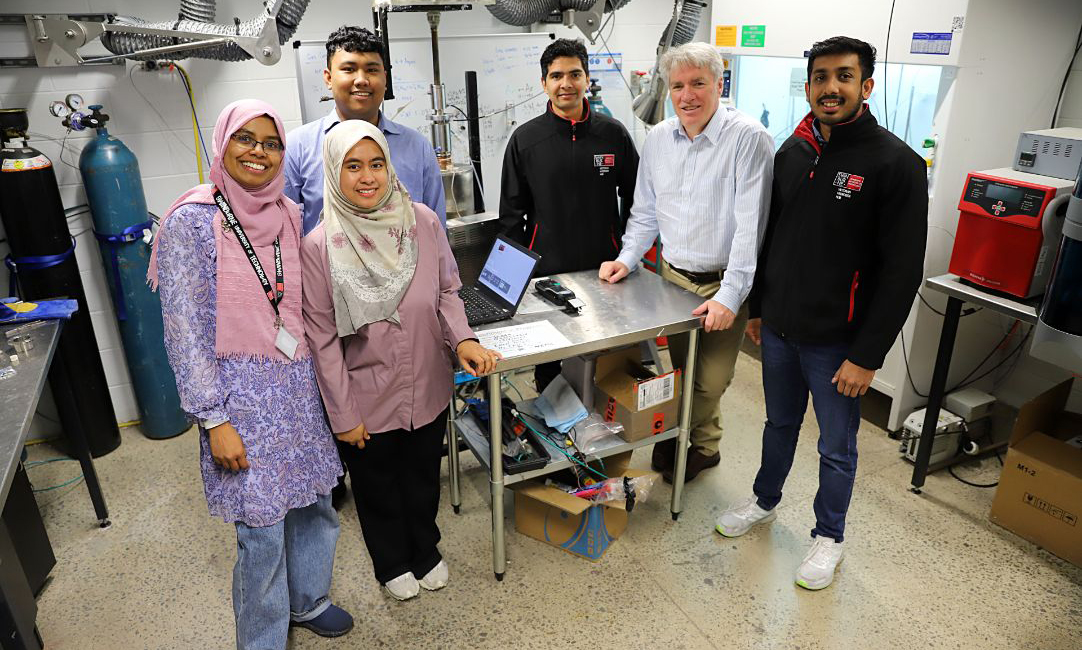
Sponsored by
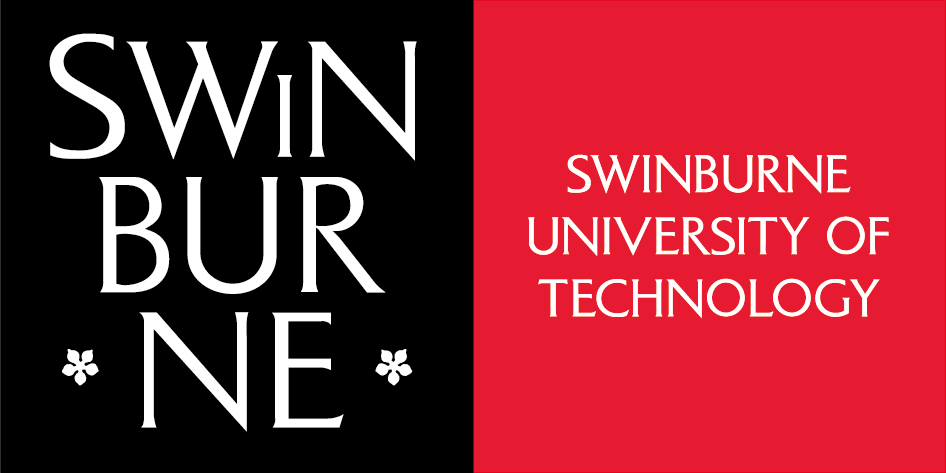
Swinburne/CSIRO joint Chair of Sustainable Mineral Processing Professor Geoff Brooks (second from right) and some of Swinburne’s green steel researchers in our High Temperature Processing Lab.
Swinburne University of Technology experts are at the forefront of the green steel revolution, developing new methods to advance a net zero emissions future through one of the world’s most widely used metals.
While steel is a fundamental building block of our modern societies, with more than 1.8 billion tonnes manufactured across the world each year, the sector is a key carbon contributor, accounting for up to 9 per cent of global carbon emissions.
Swinburne is tackling the problem by exploring green alternatives for pyrometallurgy – the processes during which metals are extracted and purified by applying heat.
Our research includes the use of magnetite ores, hydrogen, ammonia, and renewable electricity to adapt the current smelting processes, most of which centre around carbon-rich furnaces.
Working with global steel giants including Fortescue, Bluescope Steel, Infrabuild Steel and Tata Steel Europe, along with Australia’s national science agency, CSIRO, and global environmental technology company Calix, Swinburne research will deliver solutions practically and at scale.
Swinburne PhD student Tiara Triana is working with CSIRO to examine the feasibility of expanding the widely used chemical into steelmaking.
Innovating for a sustainable steel industry
One of the world’s most versatile, low cost, readily available and recyclable metals, steel is all around us – used in cars, bridges, ships, buildings, food packaging, and more.
Swinburne/CSIRO joint Chair of Sustainable Mineral Processing, Professor Geoff Brooks, said advancements in steel recyclability in recent decades have enabled more than 90 per cent of steel to be reused.
But with the manufacturing process contributing such a significant proportion of the world’s carbon emissions, there is a long road ahead to improve the sustainability of steel.
“The dominant way of making iron, which is later refined into steel, is to react iron ore with carbon materials in a high-temperature furnace,” Professor Brooks said.
“The problem is that the chemical reactions we induce through this process to create the elements of steel also result in carbon dioxide emissions that are strongly contributing to climate change.
“We need to find more sustainable ways of producing steel, because we need this material going into the future, including for infrastructure required for renewable energy, like wind turbine towers.
“But we can’t afford to keep producing so much carbon dioxide and risk environmental disaster.”
Professor Brooks and his colleagues at Swinburne are world leaders in green steel research, and among the biggest group in Australia to be tackling the issue.
“We’ve got about 20 researchers at Swinburne working in this area who are very excited, who get up early in the morning and run to work because they know they’re part of a revolution,” he said.
“This is not a theoretical exercise – this is really changing something.”
Piloting the use of hydrogen and renewable energy in steel manufacturing
Swinburne researchers are having success using hydrogen and fossil fuel-free renewable energy to replace the need for furnaces during the steel manufacturing process.
Working with Calix at the company’s Bacchus Marsh plant, the project adapts the process of direct reduction iron (DRI) in a flash reduction technology called ZESTY.
The challenge in the uptake of DRI has been in delivering it at scale in an environmentally sustainable way. Previous attempts have relied on natural gas, but Swinburne and Calix are now producing zero emissions iron and steel.
Swinburne researcher Dr Shabnam Sabah has worked on this project with Calix and Swinburne PhD students Tiara Triana, Belinda Rich and Made Giri Natha.
Dr Sabah said the research will help Australia’s iron ore industry adapt to a decarbonised future and keep pace with developments overseas.
“We investigated the effectiveness of using Australian ore in flash reduction process, which is not only important for Calix, but also Australian iron ore companies who will be selling iron ores to different hydrogen-based technologies all around the world,” she said.
“The insights from the project will help scaling and technological development of the ZESTY iron-making processes.”
Swinburne PhD student Gopal Pandey is researching the behaviour of hydrogen to mitigate risks when using the chemical to decarbonise the steel manufacturing process.
Building a hydrogen economy through the Victorian Hydrogen Hub
Swinburne’s Victorian Hydrogen Hub (VH2), a research collaboration in partnership with CSIRO and Germany’s ARENA2036, is working to drive the implementation of a hydrogen economy.
Two VH2 researchers, PhD students Gopal Pandey and Tharindu Siyambalapitiya, are also part of the push for green steel.
Gopal is researching the use of hydrogen in steel production, with a focus on understanding the behaviour of the chemical during the combustion process to mitigate risk.
“Hydrogen has potential to play a role in decarbonising the steel industry, but that must be under the right conditions or it could do serious damage,” he said.
“My research is all about furthering our understanding of hydrogen and how we can safely bring it into the steelmaking process.”
Tharindu is collaborating with sustainable steel company Infrabuild Steel, examining the use of hydrogen and induction heating in reheating furnaces during the second phase of the steelmaking process.
“The impact of this research could be transformative,” he said.
“Hydrogen and induction heating are both viable options that need to be investigated in detail to ensure its success.
“Successfully decarbonising reheat furnaces would set a new standard for the industry, potentially leading to a ripple effect of innovation in other high-emission sectors.”
Cleaning up the steel industry with ammonia
While hydrogen is favoured as a clean alternative to fossil fuels in steelmaking, it’s not without its challenges.
Swinburne PhD student Tiara Triana is working with CSIRO to examine the feasibility of expanding the widely used chemical into steelmaking.
“There are significant challenge to expanding hydrogen, including its safety issue, low volumetric hydrogen density, coupled with techno-economic challenges issues related to its transportation, distribution, and long-term storage,” she said.
“Given its efficient production process, extensive supply chain, easy handling, and established infrastructure, ammonia could potential future reductant for iron ore.”
With researchers investigating innovative solutions using a range of materials for various stages of the steelmaking process, Swinburne’s industry-led research will have wide-ranging implications beyond steel, pushing forward the critical mission for sustainable energy options across the world.