Bioplastics are vital in efforts to fight ‘wicked problem’ of plastic pollution
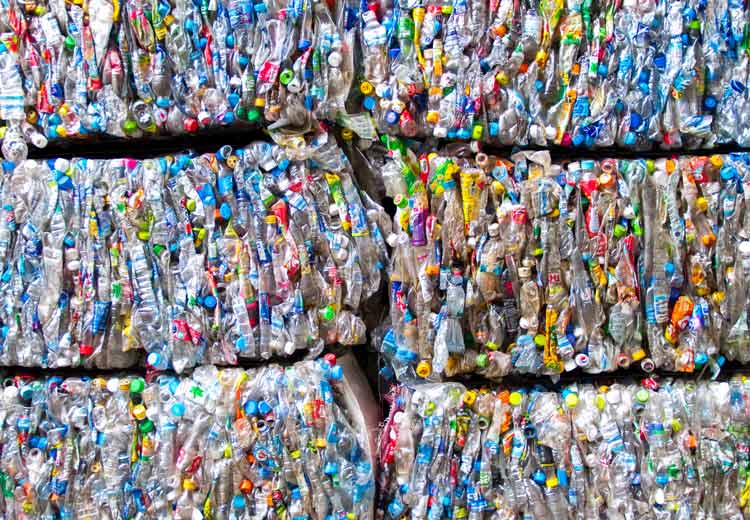
Sponsored by
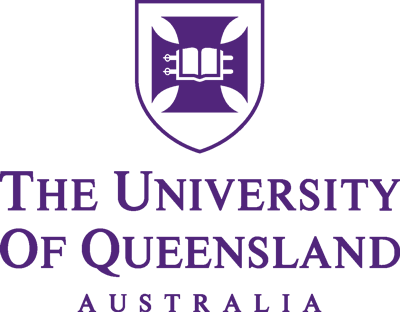
University of Queensland researchers investigate the whole bioplastics value chain, from product development to consumer acceptance
Bioplastics can help address the “wicked problem” of plastic pollution, but companies and research institutions need to take a holistic approach, says Steven Pratt, director of the University of Queensland’s ARC Training Centre for Bioplastics and Biocomposites.
Global plastic waste more than doubled between 2000 and 2019, rising to more than 350 million tonnes, according to the Organisation for Economic Cooperation and Development. It is estimated that, without intervention, this waste will triple by 2060 to 1 billion tonnes. About 40 per cent of plastic waste is from packaging.
“We are trying to make bioplastics cheaper and make sense commercially,” says associate professor Pratt, who has been working on bioplastics for more than two decades. Bioplastics is an umbrella term that includes plastics that are biodegradable, derived from biological sources rather than fossil fuels, or both.
In 2022, the global bioplastics and biopolymers market was $11.5 billion (£9.42 billion) and is projected to more than double in the next five years, driven in large part by consumer demand.
“At the Centre for Bioplastics and Biocomposites, we try to look across the value chain,” Pratt says. “We made a point of looking beyond just technology development for products.”
The centre, established in 2022, aims to promote the transition to sustainable plastics through capacity building, developing technology for new products and facilitating linkages across the value chain.
To achieve that, the centre is purposefully interdisciplinary. “We certainly have a number of lead researchers who are looking at making bioplastic products, but we also have social scientists looking at supply chains and the expectations of the market, biological scientists looking at how biodegradable plastics behave in the environment, and we also have systems engineers asking what happens if you take the biomass needed to make the products and divert it from what it’s currently used for,” says Pratt. “What does that mean for other systems we might impact?”
Meanwhile, the centre’s industry and governmental partners span the value chain, including bioplastics manufacturer Plantic Technologies, international manufacturing giant Kimberly-Clark and philanthropic organisation the Minderoo Foundation. The centre also collaborates with the Council of the City of Gold Coast and the Queensland government.
Numerous projects at the centre are investigating the various aspects of bioplastics production. “We have a research programme that seriously tackles the current barriers to widespread adoption,” he says. It includes the relationships between feedstocks, applications, markets and end-of-life impacts.
Centre researchers are also developing technologies to produce materials with the right characteristics. “Specifically, we are conducting research to make bioplastics cheaper, tougher, more readily processable and with even better barrier properties,” Pratt says.
One example is polyhydroxyalkanoate (PHA), which is already commercially available and approved for food contact. It is used for trays, cutlery and straws, and also services the eco-conscious market as material for moulded toys and eyewear frames. PHA is bio-derived and biodegradable in soil and marine, but the cheapest PHAs have a low melt strength making them difficult to blow into a plastic film, says Pratt. Sam Lawless, a doctoral candidate at the centre, has modified PHBV to improve its properties. “He has already used [his innovation] to blow films as thin as 40 micrometres [which is about half the width of a human hair] and is the desired thickness for plastic films in many film applications,” Pratt says.
Another project is looking to use bioplastics in areas where they must be biodegradable and cannot be retrieved, such as in agriculture. “One advantage offered by biodegradable polymers is the opportunity to control the release of bioactives without leaving unwanted, nondegradable residues,” says Pratt. Ian Levett, a research fellow at the centre, and PhD student Sumedha Amaraweera, built in-house coating equipment to spray-coat fertiliser granules with biopolymers to investigate the slow release of these granules as their coating degrades.
Research is inextricably linked to training and industry-readiness. Lawless, who is one of the centre’s 19 PhD students, is currently on a four-month placement with bioplastic manufacturer Plantic in Melbourne. “I aim to work for industry after completion of my PhD,” says Lawless. The placement is “providing me with valuable industry experience and connections”.
Nurturing industry-ready researchers is a vital part of the centre’s purpose. “Yes, these PhD students and early-career researchers are currently working on addressing some of today’s challenges to widespread adoption of bioplastics and composites,” says Pratt. “But, most significantly, they are being equipped to invest, design and implement the new bio-derived and biodegradable products of the 2030s and beyond.”
Pratt has big ambitions for the centre, both in terms of its research output and its commercial applications. “One ambition is a larger research group, where we look at tackling emerging challenges that the rapidly growing industry will inevitably face. Another is the commercialisation of some of the research that is already underway. On top of that, we’re also pretty keen on physically having a production facility through which we’ll be able to contribute to the global supply of PHA bioplastics,” he says.
Find out more about the ARC Training Centre for Bioplastics and Biocomposites.