Future materials
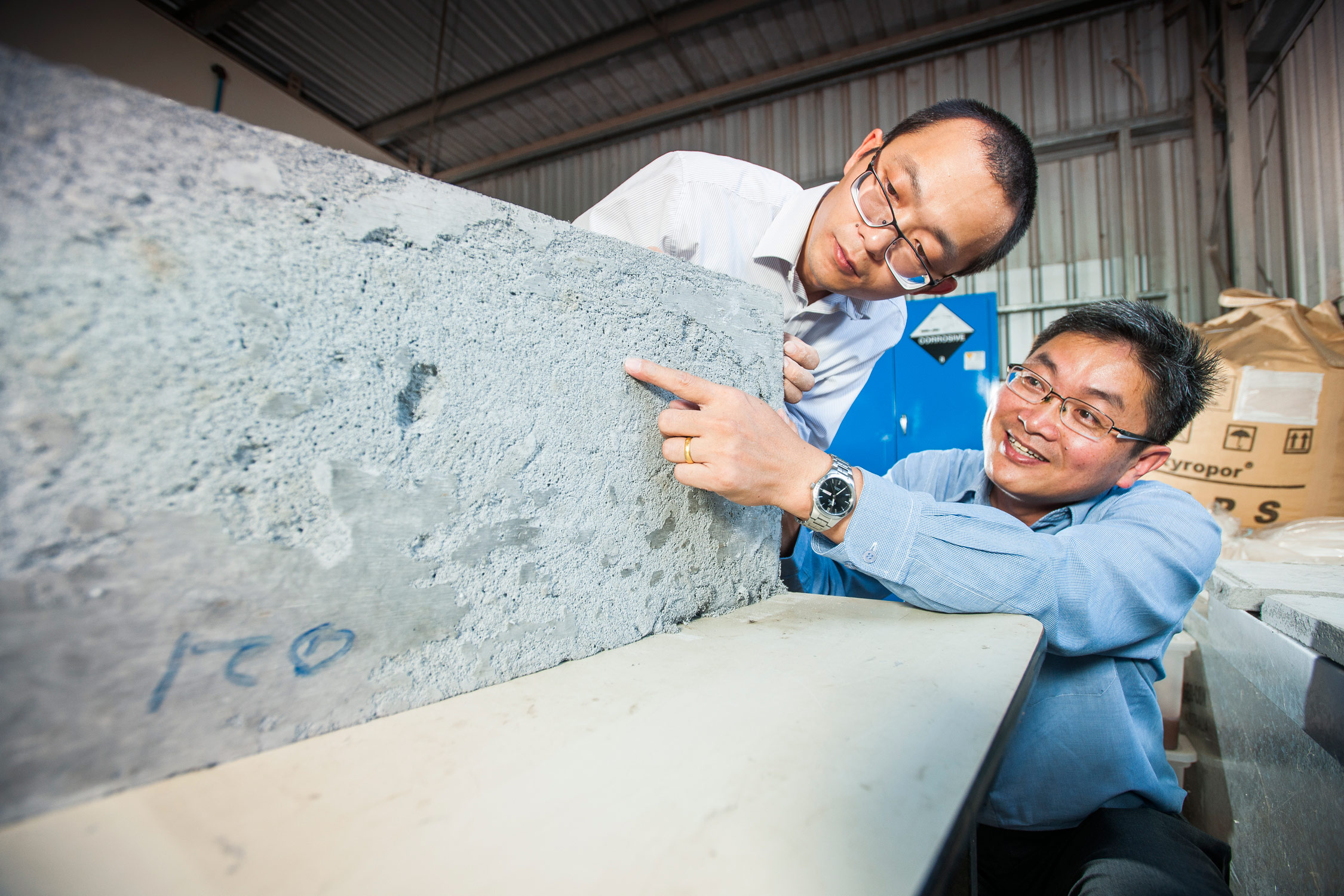
The green concrete revolution
Our modern society is built on metals, ceramics and polymers that are produced using non–renewable mineral and petroleum resources. However, it’s projected there is just enough oil to last 53 years at current production rates and therefore the race is on to develop new materials using renewable feed stocks.
Cement and concrete are the second-most used materials in the world, after water. The production of traditional Portland cement has a heavy environmental footprint, contributing to 8% of global greenhouse gas emissions. As a result, industry is being pushed to find a more sustainable way to produce cement and concrete.
Each year, Australia’s coal-fired power stations produce 14 million tonnes of fly ash, and only a very small amount is used in mostly blended Portland cement. More than a third of all ash is disposed of into dry landfills, with only 38% currently being ‘recycled’. Depending on where the coal was mined, coal and fly ash typically contain heavy and harmful metals.
Putting industrial waste to good use
Research completed by USQ’s Centre for Future Materials (CFM) has revealed that there is an opportunity to convert this high-volume industrial waste into cement. Our researchers are helping industry to manufacture high-durability green concrete with one eye on providing safe and reliable construction products.
The testing of properties of numerous grades of fly ash will help the Centre’s researchers to develop a fly ash reactivity index. This index will enable cement manufacturers (like USQ’s industry partner Nielsen’s) to evaluate the properties of the fly ash, and will indicate the amount of alkali activator needed to create a geopolymer of determinate properties.
The potential to make a positive impact on society by addressing a global issue is huge. Unlike Portland cement, geopolymer does not rely on limestone and clay, both non-renewable resources, and does not require heating to around 1450 degrees Celsius for calcination, the process which also drives out carbon dioxide. Changing the ingredients to greener options has potential to cut CO2 emissions by up to 80%. The Brisbane West Wellcamp Airport is the world’s first and largest application of modern geopolymer concrete, saving 6600 tonnes (90%) of carbon emissions by using the alternative.
A range of other industry waste products such as slag, red mud, river sludge and clay are also being investigated to innovative concretes without high temperature calcination to produce other green alternatives to Portland concrete.
Other sustainable future materials in the areas of biomass and energy materials are also going under the ‘microscope’.
Globally, more than half the heat we produce gets wasted. More than 70% of the energy produced by petroleum alone is wasted in the form of heat. Developing thermoelectric materials that convert heat to electricity provides the means to reduce non-renewable consumption, generate power for industry and personal use and substantially decrease waste in the form of heat.
There is also potential to harness strong industry linkages and international collaboration to develop thermoelectric materials which creates electricity from waste heat at any scale. This research is also making it possible to convert body heat into electricity in clothing or to provide a charge for a mobile phone.
Researchers are also working closely with Queensland industries to utilise agriculture residues, forest residues, hemp and bamboo to develop new materials and add value to agricultural and industrial waste streams. The biomass materials development includes various nature fibres, nature fibre composites, biopolymers, activated carbon, bio-chemicals and 3D printing biomass feedstock.