Advancing sustainable energy: seawater hydrogen and battery innovation

Sponsored by
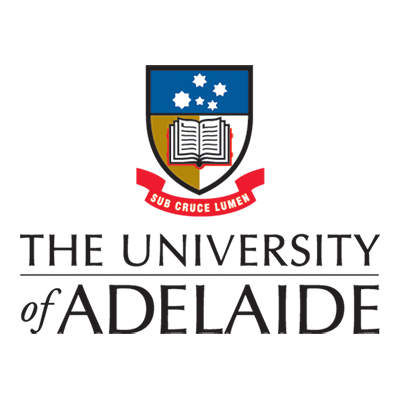
Researchers at the University of Adelaide are developing transformative technologies to drive the transition towards a sustainable energy future. Among various advancements, they are making headway in converting seawater into hydrogen fuel and enhancing battery technology to address storage requirements for a future powered by renewable energy − from electric vehicles to large-scale energy repositories.
As hydrogen takes centre stage as a promising alternative to fossil fuels, its demand is surging. Professor Shizhang Qiao, the founding Director of the Centre for Materials in Energy and Catalysis at the University, is leading research efforts to leverage seawater for sustainable hydrogen production.
"Right now, we mostly get hydrogen from chemical processes that require high pressure, temperature and a lot of energy," says Qiao.
Creating green hydrogen through water electrolysis, he says, will be crucial for reaching net-zero emissions by 2050. However, depending heavily on freshwater for this process will further strain our limited freshwater resources, prompting the need for alternative solutions.
Seawater, an abundant resource, is a viable candidate for electrolysis, says Qiao, but the current desalination methods pose a challenge: they're energy-intensive and demand super-purity water.
As existing methods fall short in producing enough water for electrolysis, he says that seawater desalination should be primarily designated for domestic, industrial, and agricultural use.
In a significant leap towards ensuring a steady supply of green hydrogen for future fuel needs, Qiao's team has found a way to tap into the vastness of the ocean.
"We've proven that we can use direct seawater electrolysis for hydrogen production without pre-treatment," he says. “Lots of research groups are focusing on this, but our approach is unique in that we’ve developed a new catalyst.”
The catalyst overcomes issues related to precipitation and chloride damage in equipment. After formulating the catalyst and incorporating new materials, Qiao’s team has successfully implemented them in a commercial electrolyser.
“The performance matched that of traditional electrolysers using high-purity water,” Qiao says.
With their sights set on bringing this technology to market, the research team is actively seeking commercialisation opportunities.
“We are currently engaging with potential investors from Australia and overseas, with a target to commercialise the technology in the next one or two years,” says Qiao.
“The first challenge is getting the funding. The second is finding enough space. We also need to be near the coast.”
In terms of the biggest challenge in the field of sustainable energy production, he says it remains to be seen “whether or not we can totally replace fossil fuel with renewable energy”.
“This depends on two factors: cost and efficiency,” he says.
In related research, Professor Zaiping Guo, also of the University of Adelaide, is focused on the development of high energy density, cost-effective, and safe batteries.
"It's essential to address the intermittent nature of renewable energy,” says Guo. “Through collaboration, we're pushing the boundaries of energy storage technology."
Having devoted two decades to this field, Guo's focus remains the same – striving for higher energy, safer designs, and reduced costs in the future of batteries.
She says that although the performance of batteries has consistently improved over the past two decades, lithium-ion remains the predominant battery type in use.
“We're currently exploring innovative battery systems like sodium-ion, potassium-ion, and zinc-ion. However, these lithium-ion alternatives are yet to be commercialised due to existing technical barriers,” she says. “Factors such as energy density, power density, cycle life, cost, and safety are essential considerations.”
Although some new battery technologies perform well in terms of energy density, they often fall short when it comes to lifespan.
“So far, new battery technologies are still not mature enough to compete with lithium-ion,” says Guo.
However, lithium-ion batteries come with their own set of drawbacks, including high cost and the use of flammable components, which present safety risks. This was illustrated during an incident at Tesla’s Victorian Big Battery site near Geelong, where two Tesla Megapacks caught fire during initial testing in 2021.
“The promise of alternatives largely depends on the application,” says Guo. “For example, cars demand batteries that have high energy density, and they are currently all powered by lithium-ion batteries. A promising alternative could be lithium metal batteries, she says, which theoretically possess about double the energy density of lithium-ion batteries.
“Right now, lithium metal batteries are mostly lab objects and there are still technical barriers to their commercialisation.”
Safety concerns and life cycle issues are the main hurdles preventing the use of lithium metal batteries in electric vehicles.
In a breakthrough that may propel lithium-metal batteries forward, Guo and her team have overcome one of the core obstacles.
“In my research, we have developed a non-flammable electrolyte that could prevent fires and explosions,” she says.
Unlike the traditional flammable carbonate electrolyte used in lithium-ion batteries, Professor Guo’s team has developed a safe electrolyte, which uses a fire retardant to dissolve the salt, rendering it non-flammable.
“This would be a promising non-flammable liquid electrolyte that doesn't compromise battery performance,” she says.
Even though numerous universities are competing in this research area, Guo believes the University of Adelaide remains at the forefront, consistently addressing key issues and devising strategies to overcome them.
“Our non-flammable electrolyte has enabled us to circumvent safety concerns,” she says. “We have patented it and have an industry partner facilitating its development. And it's compatible with existing manufacturing processes.”
Professors Guo and Qiao are leading the way in battery recycling, developing a new leaching agent that improves recycling efficiency and offers a greener alternative.
“Our work on recycling over the past two years has yielded highly encouraging results," Guo says.
Typically, a strong acid is used to dissolve the battery’s electrode material, which is corrosive, poses safety issues, and is harmful to the environment. In contrast, Guo, Qiao and their team have developed a deep eutectic solvent – which melts at a lower temperature than its individual constituents – that is safer and more environmentally friendly in place of the traditional acid.
“We have an industry partner interested in this, and we're making efforts to establish a production line in Adelaide to expedite this process,” Guo says. “Although deep eutectic solvents are being used in other labs, they haven't been used on a commercial scale yet.”
Sam Duncan
The Australian